- Overview
- Product Description
- Product Features
- Specification
- Application
- Product Details
- Product Parameters
- View of the factory
Basic Info.
Product Description
Dublok double block and bleed valve assemblies have three valves - primary isolation, secondary isolation and bleed - all integrated into a single block. If required the inlet or outlet end connection can incorporate a spring loaded in-line piston check valve. The end connectors are interchangeable and can be specified to suit exact requirements.
Our Ball valve double block and bleed assembly is very compact and is recommended for general services. The valve can incorporate Needle, Globe, Gate and Check valves into the design to suit particular duty specifications as required.
F-NPT Connecting Dbb Ball Valve(DBBQ11F) Features
Process Isolation
Drain Line Isolation
Double Block & Bleed
Blow Out Proof Stem Design
ISO 5211 Mounting Pad
Fire-safe Certified API 607
Anti-Static Device
Bi-directional Sealing
Low Fugitive Emission Packing
Locking Device Standard
Directly mounted on the flanged of piping connection ,hen the overall height is reduced.
Helps to reduce weight and cost.
Flange conncections conforming to ANSI B16.5.
Working Pressure to Flange Class.
Stainless steel construction with options of packing for high temperature application.
Colour coded dust caps for identification of valve type.
Metal to metal seating for constant compression.
Thread rolled and burnished stem.
Hardened tip for extended leak proof life.
Double Block and Bleed ball valve Applicable Specification
Design standard: ANSI B16.34 GB/T12237
Physical dimension: ANSI B16.10 GB/T12221
Flanges dimension: ANSIB16.10 GB/T15188.1
Test and inspection: API598 GB/T909
DN | 1/2"-2" | ||
Class | 150lb-2500lb | ||
Outlet | 1/2"F-NPT,3/4"F-NPT,1"F-NPT | ||
Vent | 1/2"F-NPT,1/4"F-NPT. |
F-NPT Connecting Dbb Ball Valve(DBBQ11F) Configuration
Primari Isonation | Secondary Isolation | Drain |
Ball | Ball | Needle |
Needle | Needle | Needle |
Ball | Needle | Needle |
1. The double block and bleed valve have evolved to replace and add the process of bolting together individual valves to make the valves in one body .it saved a lot of space and material.
2. Special designs including injecting quills ,sample probes ,double block and single block, in-built check valves and seat wipers.
3. Dual isolation is necessary requirement when maintenance is taking place down stream of the first isolation valve. Cavity venting is provided by either a ball or globe OS&Y vent valve so that trapped pressure between the two isolation valves is safely vented.
4. These valves have also evolved to encompass the function of chemical injection (using a suitable quill) and sample points .In-built check valves are often integrated in these valves.
5. Fire Safe according to BS6755/API 6FA/API 607, since each sealing point is provided by a secondary fire-safe seal in graphite. Valve soft seats also are provided with secondary metal-to metal seal in case of fire.
6. Valve design can be either Trunnion or floating type ,anti blow -out stem and typically SPE seat design .Drain port is normally provide with a floating ball valve ,to be fitted with final user drain line .valve seats can be soft or metal to metal hard-faced.
Applications
HP instrument connections for in line maintenance
Process vents
Process drains
Level instrument gauges
Injection points (with check)
Main Parts and Material.
NO | Part name | Material | |
GB | ASTM | ||
1 | Valve body | WCB | A2116-WCB |
2 | Sealing ring | PTFE | PTFE |
3 | Sphere | 1C18Ni9Ti | SS304 |
4 | Nut | 35 | A194-2H |
5 | Stud | 35CrMoA | A193-B7 |
6 | The stone body | WCB | A216-WCB |
7 | Shim | Graphite + stainless steel | B12.10-304F/.G |
8 | Filler | PTFE | PTFE |
9 | Packing gland | WCB | A2116-WCB |
10 | Locating piece | 25 | A105 |
11 | Ring | 65Mn | AISI 1066 |
12 | Handle | K33 | A47-667 Gr.32510 |
13 | Valve stem | 1Cr33 | A276-410 |
14 | Screw | 35 | A193-B7 |
Thrust washer | PTFE | PTFE |
Size: | 2" ~ 24"(DN50~DN400) | ||||||||
Pressure: | ANSI Ratings 150# ~ 2500# (PN16~PN420) | ||||||||
Structure: | 3 Pieces Body Design | ||||||||
Connections: | RF RTJ BW Connections | ||||||||
Body Material: | ASTM A105, A182 304, A182 316, A182 304L, A182 316L,A182 F6A,A182,F51,A182 F53,F22 Alloy | ||||||||
Ball Material: | ASTM A105, A182 304, A182 316, A182 304L, A182 316L,A182 F6A,A182,F51,A182 F53,F22 Alloy | ||||||||
Seats Material: | PTFE/ RTFE(≤120ºC) , NYLON (≤80ºC), PEEK/PPL (≤250ºC) | ||||||||
Driving means: | Manual,worm gear.etc. | ||||||||
Flow direction: | bidirectional | ||||||||
Applicable medium: | Seawater,all kinds of harsh environment |
Design basis | GB series | American Standard Series | |
Design standard | GB/T12237 | AP16D | ANSI B16.34 |
Flange connection structure length | GB/T12221 | AP16D | ANSI B16.10 |
The length of the structure ( welding ) | GB/T15188.1 | AP16D | ANSI B16.10 |
Connecting flange | GB/T9113 JB/T79 Hg20592 | ANSI B16.5 | |
Butt welding ends | GB/T12224 | ANSI B16.25 | |
Test and inspection | GB/T9092 | AP16D | AP1598 |
Main Dimensions
Nominal diameter | 15 | 20 | 25 | 40 | 50 | 65 | 80 | 100 | 125 | 150 | 200 |
d1 | 13 | 19 | 25 | 38 | 64 | 64 | 76 | 102 | 127 | 152 | 203 |
L | 108 | 117 | 127 | 165 | 191 | 191 | 203 | 229 | 356 | 394 | 457 |
H | 59 | 63 | 75 | 95 | 142 | 142 | 152 | 178 | 252 | 272 | 342 |
W | 130 | 130 | 160 | 230 | 400 | 400 | 400 | 650 | 1050 | 1050 | 1410 |
Wt(kg) | 2.5 | 3 | 5 | 7 | 15 | 19 | 19 | 33 | 58 | 93 | 160 |
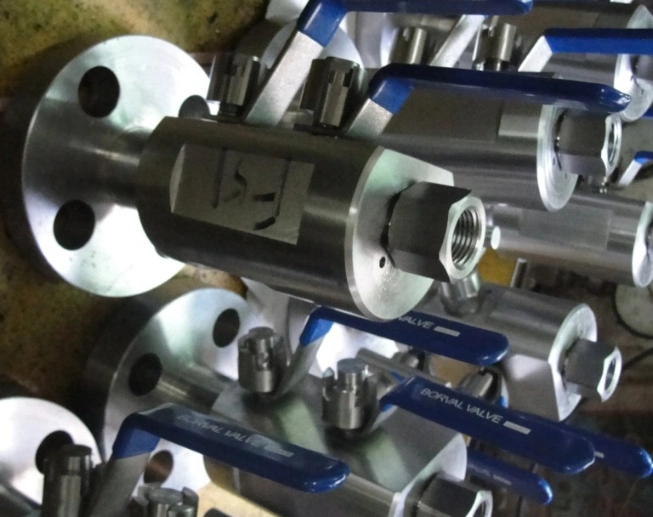
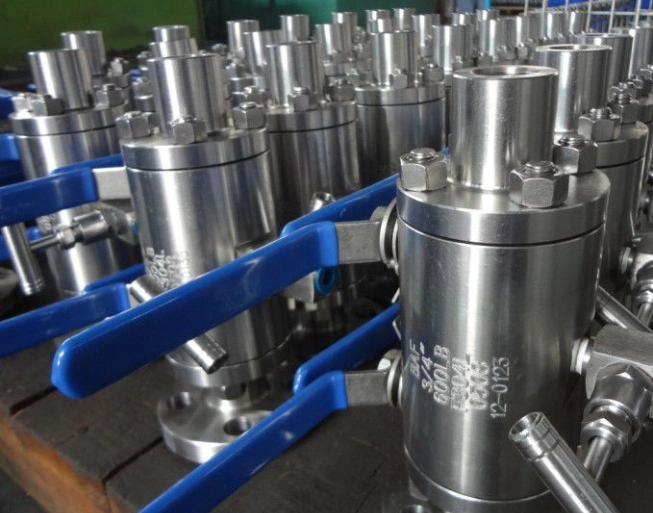
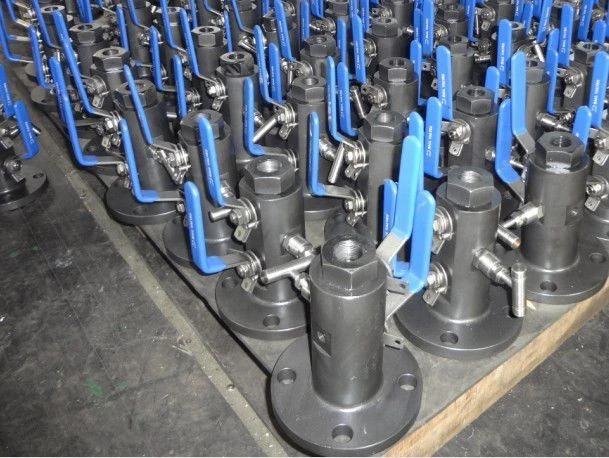
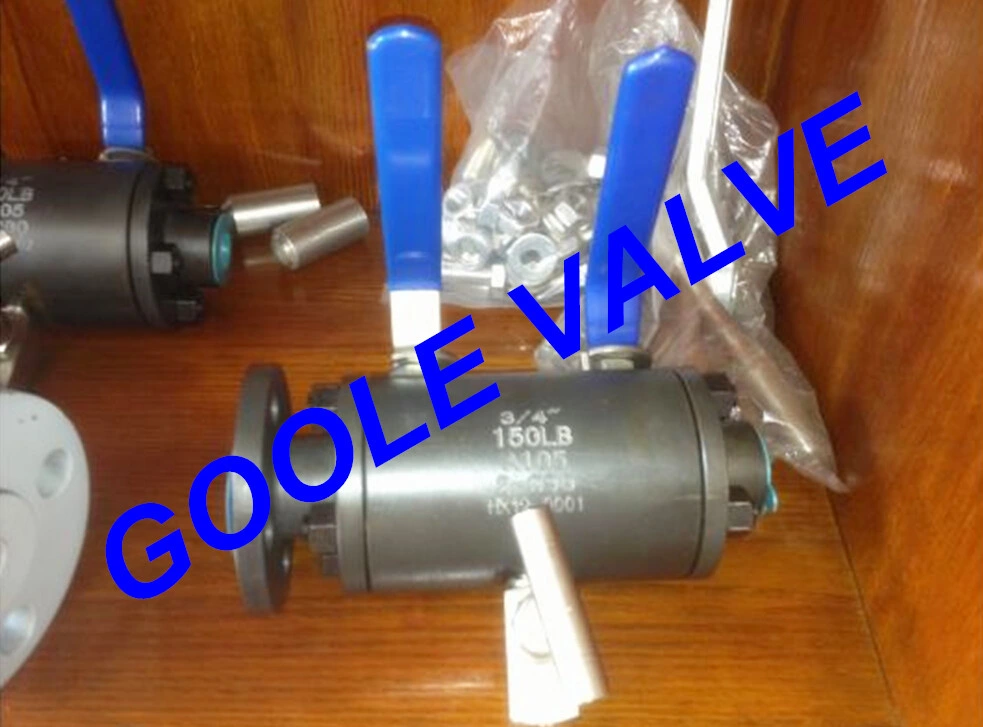